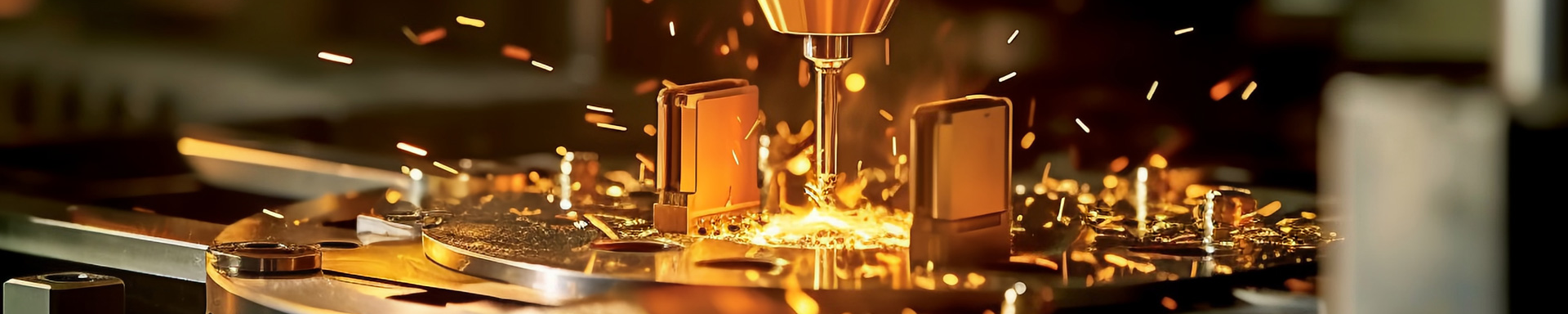
Técnicas avanzadas en procesos de fundición a presión de automóviles
2024-11-22 15:41Mejoras en la fundición a presión a alta presión (HPDC)
La fundición a alta presión (HPDC) sigue siendo una piedra angular de la producción de componentes automotrices, apreciada por su velocidad y capacidad para crear piezas complejas. Sin embargo, la HPDC tradicional a menudo tiene dificultades para lograr una precisión dimensional y una calidad de superficie constantes en lotes grandes. Las mejoras modernas se centran en optimizar todo el proceso, desde el diseño de la matriz y la selección del material hasta los parámetros de inyección y las técnicas de posprocesamiento. Esto incluye avances en los materiales de la matriz que ofrecen una resistencia al desgaste y propiedades de transferencia de calor superiores, lo que conduce a una vida útil prolongada de la matriz y una mejor calidad de las piezas. Además, la implementación de sofisticados sistemas de control permite un monitoreo y ajuste precisos de parámetros como la presión de inyección, la velocidad y el tiempo de retención, lo que minimiza las variaciones y garantiza resultados consistentes.
Otro aspecto crítico de mejora es el uso de software de simulación. Estos programas avanzados permiten a los ingenieros probar virtualmente varios diseños de matrices y parámetros de inyección antes de que comience la producción real. Esta capacidad predictiva reduce significativamente la necesidad de realizar prototipos físicos costosos y realizar iteraciones, acelerando el proceso de desarrollo y minimizando los desechos. La integración de sensores sofisticados dentro de la máquina de fundición a presión proporciona información en tiempo real, mejorando aún más el control del proceso y optimizando el resultado. Este enfoque basado en datos conduce a mejoras significativas en la calidad de las piezas, reduciendo los defectos y aumentando la eficiencia general.
Fundición a presión de pared delgada
La demanda de vehículos ligeros está impulsando una fuerte tendencia hacia la fundición a presión de paredes delgadas. Esta técnica permite la creación de componentes con espesores de pared significativamente reducidos, manteniendo al mismo tiempo la integridad estructural. Esto no solo contribuye a la reducción de peso, sino que también reduce los costos de material. Sin embargo, lograr una fundición de paredes delgadas requiere un control preciso sobre el proceso de inyección y el uso de matrices especializadas. Las técnicas avanzadas emplean diseños de matrices optimizados con sistemas de enfriamiento mejorados para garantizar una solidificación rápida y evitar defectos como porosidad o deformación. El desarrollo de aleaciones de aluminio de alta resistencia específicamente adecuadas para aplicaciones de paredes delgadas mejora aún más la viabilidad y la resistencia de estos componentes.
El proceso también se beneficia de las innovaciones en el diseño de matrices, que incorporan características como sistemas de compuertas optimizados y estrategias de ventilación para mejorar el flujo de metal y minimizar la acumulación de aire. Las simulaciones avanzadas desempeñan un papel crucial en la predicción de posibles problemas y la optimización de los parámetros del proceso para lograr la geometría de pared delgada deseada, manteniendo al mismo tiempo la integridad estructural y la calidad de la superficie. La implementación de sistemas de control y monitoreo en tiempo real minimiza aún más los defectos y garantiza una producción constante de componentes de alta calidad.
Fundición a presión de múltiples materiales
La integración de múltiples materiales en un único componente de fundición a presión abre posibilidades interesantes para mejorar la funcionalidad y el rendimiento. Este enfoque permite la combinación de materiales con diferentes propiedades, como resistencia, conductividad térmica y conductividad eléctrica, en una única pieza. Por ejemplo, un componente podría incorporar un núcleo de aleación de aluminio de alta resistencia para lograr integridad estructural, combinado con un material más blando y dúctil en áreas específicas para mejorar la funcionalidad o reducir el desgaste. Esto requiere un diseño de matriz sofisticado y un control preciso del proceso de inyección para garantizar la colocación y unión precisas de los diferentes materiales.
Las técnicas avanzadas de fundición a presión de múltiples materiales a menudo implican el uso de insertos especializados dentro de la matriz para definir los límites de los diferentes materiales. El control preciso de los parámetros de inyección es crucial para evitar la mezcla o delaminación de los diferentes materiales. El uso de software de simulación es particularmente crítico para optimizar el diseño y los parámetros del proceso, asegurando la integración y unión exitosa de múltiples materiales dentro del componente final. El desarrollo de nuevas técnicas de unión, como la soldadura por fricción y agitación o la unión por difusión, también está desempeñando un papel importante en la creación de fundiciones de múltiples materiales robustas y confiables.
Materiales y recubrimientos avanzados para matrices
El rendimiento y la longevidad de las matrices de fundición a presión afectan significativamente la eficiencia y la calidad generales del proceso. Los materiales tradicionales para matrices, si bien son funcionales, suelen presentar limitaciones en términos de resistencia al desgaste, conductividad térmica y resistencia a la corrosión. Los avances modernos se centran en el desarrollo y la aplicación de materiales innovadores para matrices, como aleaciones de acero avanzadas, compuestos cerámicos y recubrimientos novedosos. Estos materiales brindan una mayor durabilidad, lo que permite mayores tasas de producción y una vida útil más prolongada de las matrices.
Los recubrimientos especializados, aplicados a la superficie de la matriz, mejoran aún más la resistencia al desgaste, reducen la fricción y mejoran el acabado de la superficie de los componentes fundidos. Estos recubrimientos se pueden adaptar a aplicaciones específicas y ofrecen propiedades personalizadas, como una mejor transferencia de calor o características de liberación. El desarrollo de recubrimientos más duraderos y confiables está en curso, con el objetivo de lograr una resistencia al desgaste aún mayor y mejorar la calidad general de las piezas fundidas. Esto permite mayores tasas de producción y una mejor calidad de los componentes, al tiempo que minimiza el tiempo de inactividad asociado con el mantenimiento y el reemplazo de la matriz.